Let’s cut through the hype: choosing the right fiberglass cloth for resin projects isn’t about grabbing the cheapest roll or the heaviest weave. It’s about matching weight to purpose and avoiding rookie mistakes that turn your masterpiece into a flimsy mess. Below, I’ll break down the best fiberglass cloth for resin and pit fiberglass weights head-to-head—because if you’re spending hours laminating, you deserve results that won’t crack, warp, or waste resin.
The Fiberglass Weight Showdown: Thin vs. Thick vs. Goldilocks
Fiberglass cloth weight (measured in ounces per square yard) dictates strength, flexibility, and resin absorption. Here’s the brutal truth:
Weight (oz/yd²) | Thickness (mm) | Tensile Strength (MPa) | Ideal For | Resin Hog? |
---|---|---|---|---|
4 oz | 0.10 | 300 | Small repairs, curved surfaces | Low |
6 oz | 0.18 | 450 | Boats, automotive parts | Moderate |
10 oz | 0.25 | 700 | Structural panels, heavy-duty FRP | High |
My take:
- 4 oz cloth is your go-to for delicate work like surfboard repairs or sculptural art. It conforms to curves like a dream but lacks backbone—don’t trust it for load-bearing parts.
- 6 oz cloth strikes the sweet spot for most DIY projects. I’ve used it for kayak hulls and motorcycle fairings; it balances strength and resin efficiency without feeling like concrete.
- 10 oz cloth is overkill unless you’re building a submarine. Yes, it’s strong, but it’ll guzzle resin and leave your project stiff and prone to air pockets if you’re inexperienced.
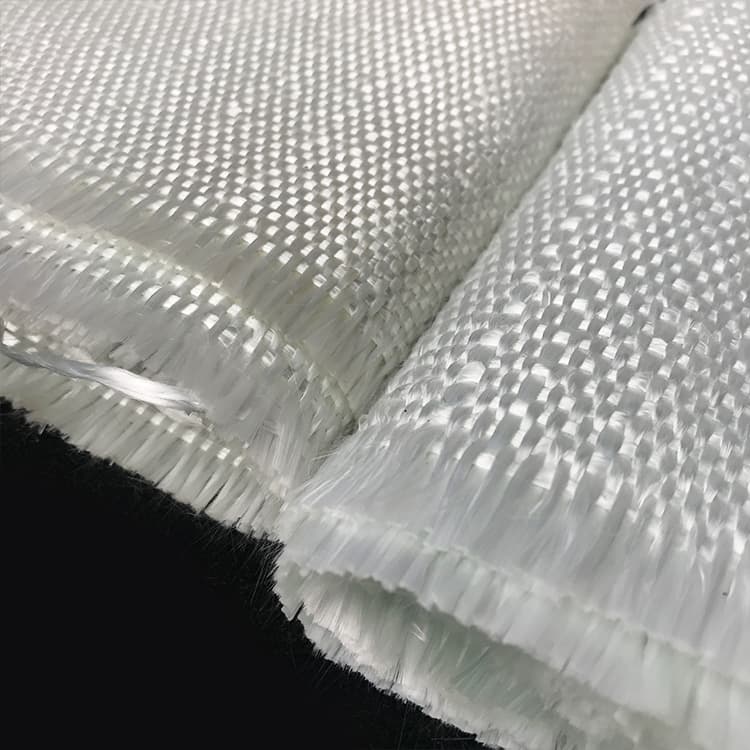
the Best Fiberglass Cloth
The ‘Best’ Fiberglass Cloth for Resin? Depends on Your Enemy
The “best” cloth isn’t universal—it’s about defeating your project’s arch-nemesis:
- Enemy: Flex Failure → 6 oz biaxial weave
- Example: Repairing a boat transom? Biaxial (±45° fibers) resists multidirectional stress better than plain weave. I’ve seen plain weave crack along the grain under engine vibration; biaxial laughs at torque.
- Enemy: Resin Waste → 4 oz tight weave
- Example: Coating a decorative tabletop? A tight 4 oz weave minimizes resin absorption while still adding scratch resistance. Open weaves (like 10 oz) soak up epoxy like a sponge—budget killers.
- Enemy: Delamination → Silicone-coated cloth
- Example: High-moisture environments (e.g., bathroom panels)? Silicone-treated cloth resists water ingress. I’ve ripped standard cloth off shower stalls after 6 months; treated cloth lasts years.
The One Mistake Everyone Makes (And How to Avoid It)
Ignoring weave density. A 6 oz cloth with a loose weave behaves like a heavier weight but with weaker interlaminar bonds. Always check threads per inch (TPI):
- 50+ TPI: Good for vacuum bagging (less resin pooling).
- 20–30 TPI: Better for hand layup (easier air bubble removal).
At a recent maker fair, I watched someone use 6 oz/20 TPI cloth for a carbon fiber-esque drone arm. Result? Resin-rich zones snapped under stress. Higher TPI would’ve distributed load evenly.
Final Word
Stop overcomplicating this. For 90% of resin projects: 6 oz biaxial cloth is your MVP. Save 4 oz for art and 10 oz for NASA prototypes. And for the love of all things cured, test a scrap piece first—because nothing stings like a botched project and a half-empty resin jug.